Abstract
Metal scrapers, which do not scratch uncoated glass, are used by window cleaners throughout the world to clean quality uncoated tempered and annealed glass surfaces in an efficient, effective, environmentally friendly manner. Metal scrapers are also commonly used within the glass, painting and automotive industries.
Some tempered glass, however, scratches easily during cleaning, as a result of having travelled on furnace rollers contaminated with glass fines. The roller side then bears numerous fine defects which cause scratches when cleaned with a common metal scraper. Complaints of tempered glass scratching this way are widespread in the US market, though not unheard of in other markets.
The author proposes a simple surface quality test using a standard window cleaning scraper and common smartphone or shop microscope. His presentation is intended to increase awareness and promote the discussion and resolution of tempered glass roller side defects.
Introduction
Numerous microscopic roller side defects are caused when tempered glass is processed on furnace rollers contaminated with glass fines; these defects in turn cause numerous fine scratches during cleaning with common metal scrapers.
A few of these microscopic defects is no problem – a surface with too many defects will scratch badly. By our count, this is the 9th paper presented at GPD to discuss roller side problems related to glass fines, and the 5th to discuss the glass fines/scratch problem. We hope to further the discussion. Does your company have a plan to minimize this problem?
Glass Fines
Scratch-causing roller side defects are a result of microscopic glass fines entering the furnace - perhaps on unwashed or poorly washed glass. Infrequent cleaning of rollers may contribute to the problem. Everyone understands this should not occur to excess, but too often it does occur. How closely is this monitored?
Do frontline people understand? Particles on furnace rollers have the weight of softening glass pressing against them, and may cause a surface defect. The defect might be mechanical damage (a chip or a bump) - or the particle may be transferred from the roller to the glass.
There are many rollers in the heating chamber of a horizontal furnace, and every particle on a roller will touch the glass several times. It’s easy to see how a glass fines problem can get out of hand on the roller side, while the top may be unaffected. (There is no roller side issue for older vertical furnaces, and newer gas hearth furnaces.).
Scratches
When a moving scraper encounters a microscopic fabricating debris defect during cleaning, there are several possible outcomes. Often there is no scratch; a finer defect might be passed over without incident, the defect might be broken or dislodged, but suspended in cleaning solution.
A defect might be trapped under the blade in a way that causes only minor abrasion without indenting the surface. None of the above are cause for concern. Often, however, a fabricating debris defect may be trapped by the moving scraper in a way that will indent the surface, causing a fine scratch with lateral chipping that may become visible.
In worst cases, due to excessive numbers of defects, a multitude of these fine scratches are created, and become visible due to sheer numbers. [Figure 1]
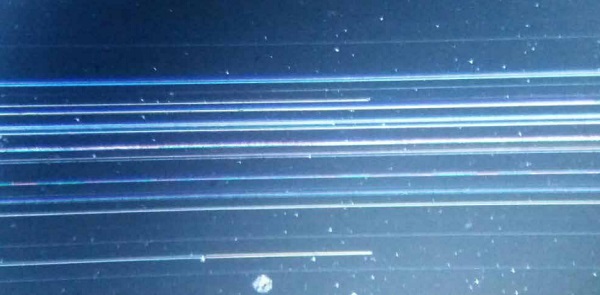
Control
The best way to minimize our roller side glass fines/scratch issue is to control glass fines at the source. Perfection is unnecessary; however, poor quality surfaces are far from perfect. At least 11 microscopic defects are visible [Figure 2] - in a field of view smaller than 5mm square. For a tempered lite the size of a GPD poster (1m x 1.2m) this would project to 500,000 or more defects.
Much has already been written about particles and rollers with respect to a visible roller side defect - white haze. Tempering experts routinely advise fabricators to prevent particles from entering the furnace, to ensure the quality of edgework, to temper only clean glass, to keep furnace rollers clean, and keep the area around the furnace clean.
We realize particles are not the only contributor to white haze issues, but this advice is applicable to the glass fines/scratch issue as well.
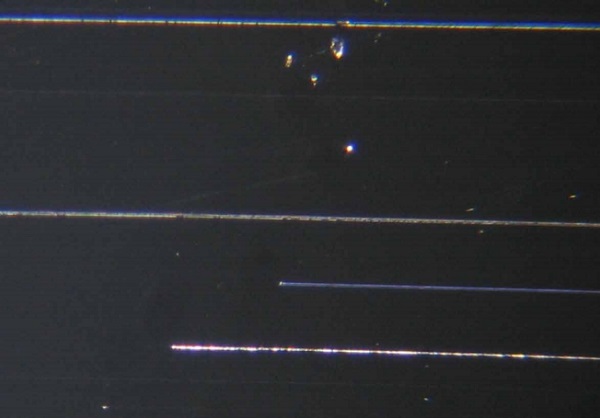
Field Testing
The old advice for cleaners to test a cleaning method in the field and look for damage is not practical in the matter of scrapers versus glass fines. These microscopic particles cause scratches that may be microscopic at first - invisible to the naked eye for hours.
This is because, due to time delayed scratch growth, microscopic scratches may become 10 times wider several hours later; thus an invisible scratch 10-20 microns wide may become visible hours later (at 200-300 microns wide). To perform a field test, cleaners would need to test representative samples of all glass with scrapers and wait a day to check for damage, or examine each with a microscope. Is this a reasonable expectation?
Monitoring
There are ways a fabricator monitor their own efforts to minimize glass fines and defects that cause scratches during cleaning. Unlike some other well-known quality issues, glass fines generally can’t be seen. So how can managers, furnace operators and quality controllers monitor efforts to meet quality objectives?
A simple test can be done using a wide window cleaning scraper on tempered glass to simulate the effects of future cleaning. This test attempts to cause fabricating debris scratches which can be observed with a smartphone camera and clip-on microscope, or a common shop microscope. Anyone in the organization can do this test.
Equipment needed
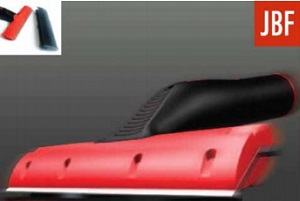
Felt tipped marker
Straight edge
Lighted shop microscope – 40x - 100x
Smartphone camera with microscope attachment
Conveniently located testing area
6 inch glass cleaning scraper such as the Triumph MK3. [Figure 3]
Method
Obtain test lites at furnace unload; label each with relevant information such as date and time.
Always test the roller side.
Test promptly, while the glass is clean. If you’ll be testing later, be sure to clean the glass again. (When the glass is clean, use of water is optional.)
Draw two parallel lines 6 inches apart with a felt tipped marker, from one edge to the other. Place the scraper between the lines, near one edge.
Apply firm pressure and push the scraper completely across the glass – try to cause scratches. [Figure 4]

Observations
After scraping, use the microscope to observe the scraper’s edge. Note whether any debris has accumulated. [Figure 5]
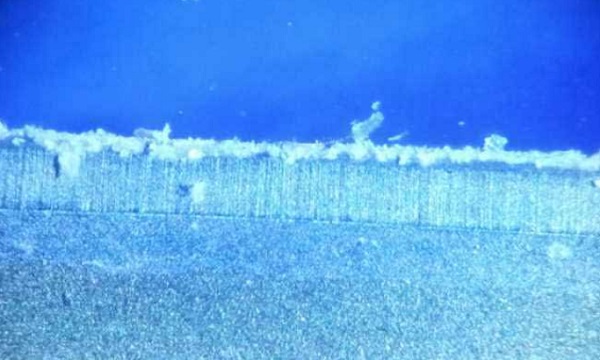
Use the marker to draw a perpendicular line across the path of the scraper.
Scratches are more numerous toward the end of the path than at the beginning.
Place the microscope on one end of that new line.
Turn on the light, and rotate the scope so light shines perpendicular to the path.
Focus the shop microscope on the line.
Slowly move the microscope along the line, from one end to the other.
Try to count every scratch that intersects the line you’ve drawn [Figure 6].
Enter result in a log, and report any unusual results promptly.
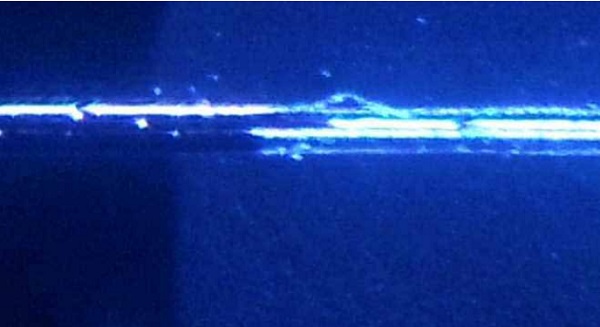
Comments
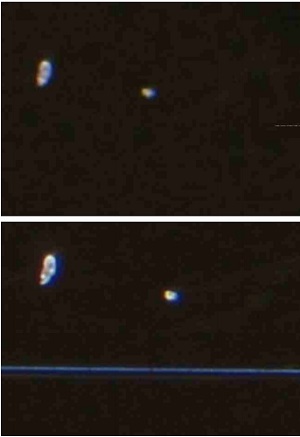
Scratches will occur immediately, but it takes hours for scratches to be fully realized. Scratches which are difficult to find at first, might be visible the next day.
You may see more defects than scratches, and more microscopic scratches than visible scratches. On quality surfaces, defects will be scarce, microscopic scratches will be rare and visible scratches rarer still.
Proper illumination is essential. Keep the light perpendicular to scratches. [Figure 7]
The microscope may be used to follow any scratch to the point of origin. Often an interesting defect will be seen at the point of origin that may help inform troubleshooting efforts. [Figure 8]
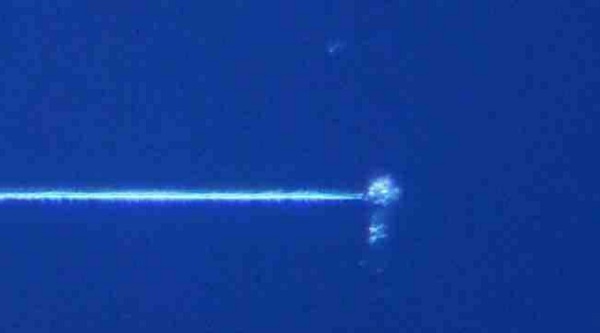
Conclusions
We urge glass tempering experts to turn their attention to the glass fines/scratch problem and develop literature, training, software modules, etc. specific to this issue. Glass tempering technology has advanced to the point where powerful software can control processes, and laser marking tracks the history of every lite tempered.
We urge fabricators take advantage of resources find available to them. As mentioned, articles about white haze tend to have excellent advice about keeping particles out of a furnace. An unprecedented number of resources are available online. Search for the Glass Tempering Handbook.
The professional networking site LinkedIn has several glass discussion groups; some have thousands of members. There are excellent articles on tempered glass issues online at www.glassfiles.com, www.glastory.com and elsewhere online. Equipment manufacturers are good sources of information.
The most difficult way to get feedback on roller side quality is dealing with reports of glass scratching in the field. The best way to know if your operation would benefit from a renewed emphasis on plant cleanliness, tempering practices, and equipment maintenance is to check in house for scratch-causing roller side defects.
Testing can help a fabricator discover and resolve quality issues internally, possibly without resorting to expensive forensic methods such as scanning electron microscopy and energy dispersive spectroscopy. The small cost of monitoring should be recoverable through sustained productivity, extended useful life of equipment, and a general reduction in costs associated with scratched tempered glass.
The world uses scrapers to remove foreign matter (cleaning, glass and other industries) and the world knows scrapers don’t scratch uncoated glass. Attempts to convince the world to use slower and more labor intensive means don’t seem to be working. Will that change any time soon? There will be always be demand for safe, practical, effective cleaning methods, and for glass that can be cleaned with scrapers.
Author
Gary Mauer is Director of the Window Cleaning Network, member of MWCoA, and a founding member of the International Window Cleaning Association. His 38 year career in the window cleaning industry was preceded by 3 years experience with a glass fabricator.