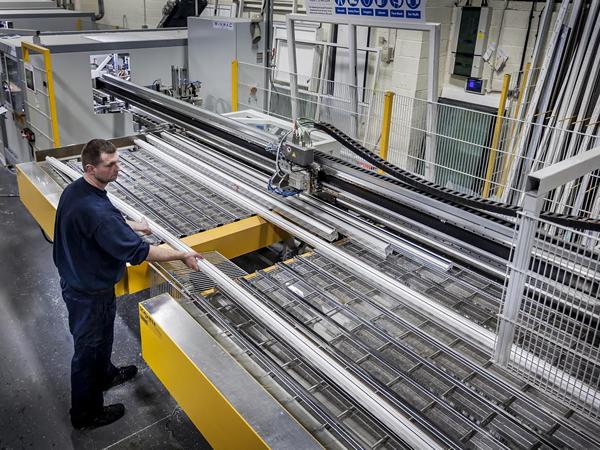
This includes the purchase of a new Rotox eight-head welder and cleaning line, giving Emplas two fully automated lines.
It’s also invested in a new Rotox high speed sash cleaner, increasing sash output by more than 20% and a Rotox five-head inline welder, giving Emplas a total of three five-head welders and one four-head welder.
A second Rotox crucifix welder is also added to Emplas’ machinery inventory, as are two new Rotox bead lines and a second Schirmer machining and cutting centre.
This automates profile cutting and machining, with profile scanning technology to introduce ‘pin prick’ accuracy to positioning of cuts and routs to within 0.3mm. It delivers improved product quality but able to convert a 6m bar length into a fully prepped frame within seconds, it also massively increases Emplas’ production capacity.
Ray Sinclair, Operations Director, Emplas, said: “The investment we’re making gives us more capacity but it also allows us to drive continuous improvements in our product quality and service.
“We’re looking to grow but to grow sustainably and that means investment in our manufacturing capability, the increased accuracy, efficiencies and productivity that new machinery gives us, allows us to not only improve end quality of product but lower our own overheads and mitigate material costs, benefits, we’re passing directly on to our customers.”
In addition to machinery investment a major extension of Emplas’ operational hub is already well underway. Scheduled for completion in the autumn, it will give the fabricator 18,000 sq ft of additional floor space.
Adding around a third again to Emplas’ manufacturing facility, the new development will also house loading bays and offices.
This investment in machinery and square footage has also been underpinned by a corresponding investment in its IT infrastructure, linking production to its ordering processes, customer tools, as well as increasing visibility of production to Emplas customer services teams.
Sinclair added: “We’re working to improve our workflows, our product quality and the visibility of those processes within our own organisation but also to our customers.
“The machinery investment that we’re making is important but only a part of that wider story. We’re connecting everything, allowing us to deliver ever improving standards of product quality but also improved service to our customers.”